06 December 2016
D-Drill was approached by VolkerHighways early in 2014 to determine the feasibility of cutting a 45degree splay on insitu granite and concrete kerbs as part of the installation of the major new Cycle Superhighway in London.
This innovative method would remove the requirement of excavating and disposing of up to 66km kerbs and replacing them new bespoke kerbs procured from China on a 12 week lead in time, therefore reducing disruption, cost and time.
D-Drill investigated the world markets through their connections in the International Concrete Drillers and Sawers (IACDS) and discovered there wasn’t a machine in existence to carry out these works.
Seeing a gap in the market around cycle-paths and size of the Cycle Superhighway alone, D-Drill decided to see if a machine could be invented that could do it!
After months of research and development and using their years of experience in concrete cutting – the first prototype was developed and trialled in D-Drill’s Coventry Head Office.
The first prototype was a success and the decision was made to make further developments on the machine.
After the developments were made, including the use of “Silent Diamond Blades” a further demonstration was proposed. VolkerHighways built a mock up footpath in their Enfield Depot, amongst some the attendees were Transport for London (TFL), other LoHAC contractors and other representatives from local London Boroughs.
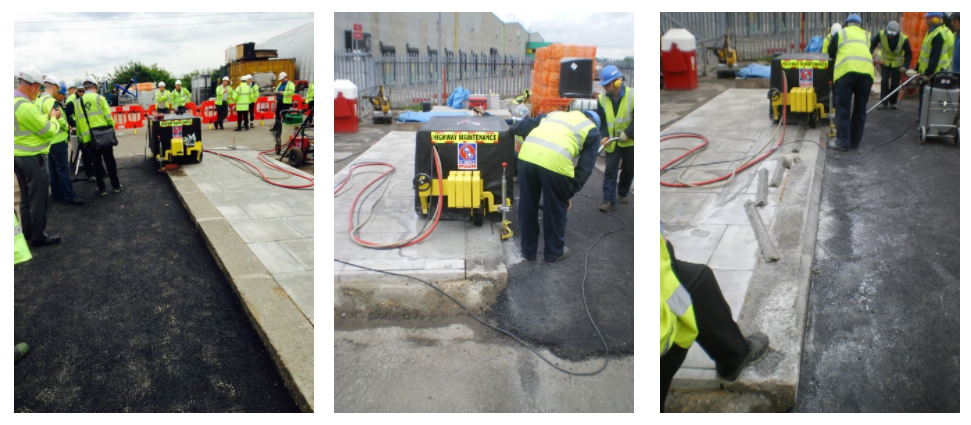
Once again the demonstration was a success, and all the comments from the day were taken on board to aid in developing the cutting machine, however one last jigsaw in the puzzle was still to be found, how the sawn face can be redressed to match the other parts of the existing kerb.
A piece of sawn granite was sent to America to see how a vapour blasting machine would redress the kerb. After the trials in America, the piece was returned to England for inspection, and the results were better than expected and the added bonus was that this methodology is also better for the environment as it reduces water waste and improved health safety around HAV.
The first real test for the cutting and Vapour blasting machine was to be undertaken on a contract to cut 30 metres of granite kerb in Denman Street just off Piccadilly Circus outside a boutique hotel on behalf of Westminster City Council & WSP, the works were carried out and completed within two hours to the complete satisfaction of Westminster City Council (WCC) and their Engineers WSP.
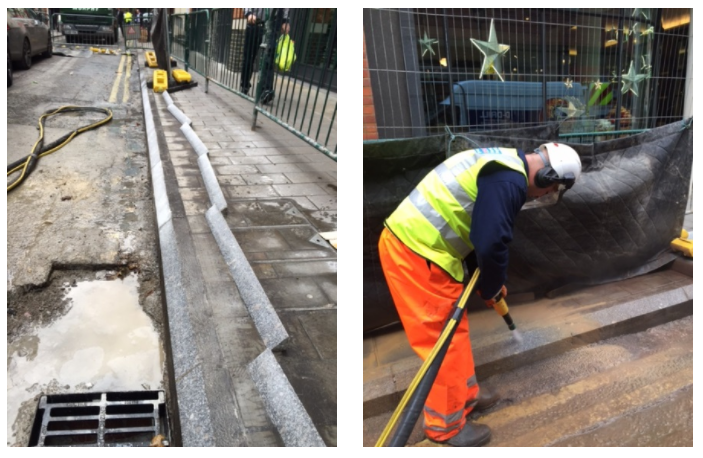
As can be seen in the photographs above, both the cutting and redressing of the granite kerb was carried out without the expensive yorkstone and pavement being taken up. Note the carriageway was in the process of being resurfaced.
Following the first job in Denman Street, a similar job, outside the Café Royale in Air Street, London, was undertaken; the existing 90 degree kerb was causing difficulties for vehicles dropping off due to the narrow road.
WCC didn’t want to have to close that part of the road for several days to replace the kerbs with new granite splayed kerbs, which were also on a long lead in.
By utilising the D-Kerb, our team cut and redressed the kerb in just a matter of hours, solving the problem. It cut the kerb while shoppers and tourists went about their business uninterrupted and saved tens of thousands of pounds.
The D-Kerb was most recently used on the Cycle Superhighway 6, better known as North South in several areas along the route including a section directly outside TFL’s Palestra Office.
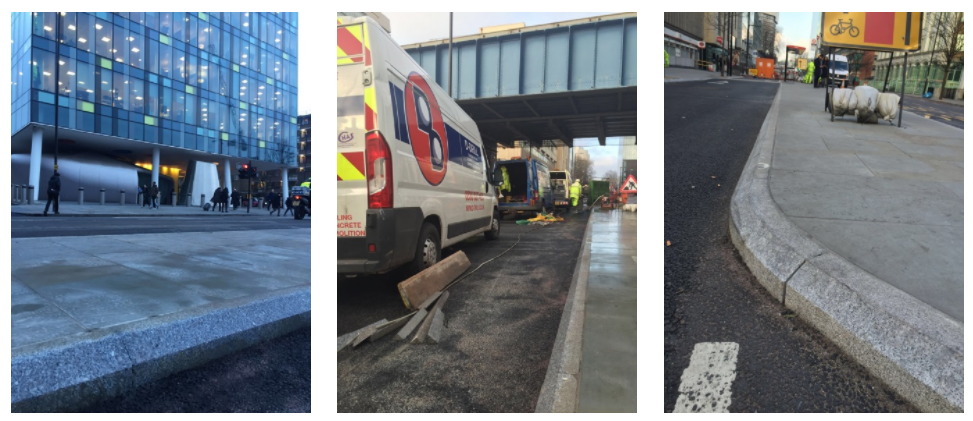
To summarise, the machine has saved many hundreds of thousands of pounds, time, tonnes of waste, reduction in Co2 Emissions, as can be seen below in the table prepared by Encraft Ltd:
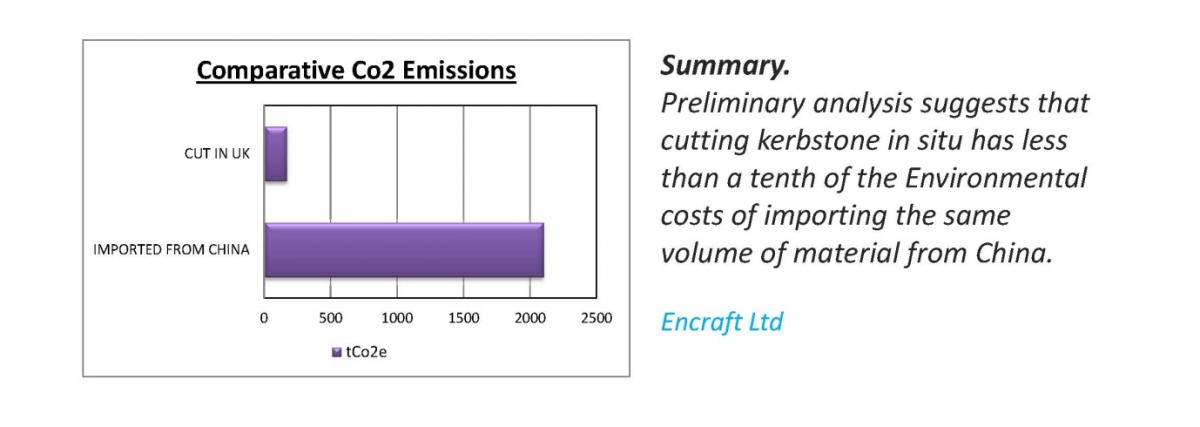
The trials and works carried out to date have shown that D-Kerb has significant advantages, making the months of research and development worthwhile.
Back to news